Introduction
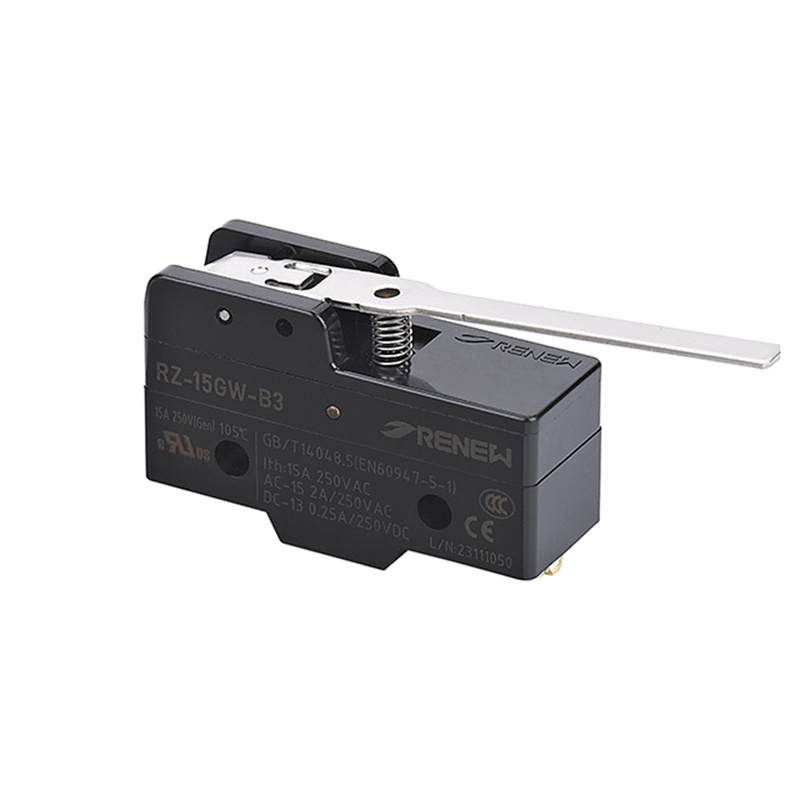
In industrial automation equipment and consumer electronic products, micro switches, as key control components, their lifespan performance directly affects the overall reliability of the equipment. Many users tend to confuse "electrical life" with "mechanical life", but in fact, these two indicators have essential differences: mechanical life refers to the number of pure mechanical actions of a switch under no-load conditions, such as the number of times a key is pressed daily. High-quality products can reach over ten million times. The electrical life, on the other hand, refers to the number of times a current-carrying circuit is disconnected under rated load, which is typically only 10% to 50% of the mechanical life. This is because the arc generated when the contacts are turned on and off accelerates metal oxidation and material loss.
Analysis of Test Standards
At present, the industry generally follows international and domestic standards such as IEC 61058-1 and GB/T 15092.1 for testing. Mechanical life tests require continuous operation at a specified frequency (15-60 times per minute) under no-load conditions to verify the durability of the structure. Electrical life testing requires operation under rated voltage (≤480V) and current (≤63A). Different load types, such as motors and bulbs, have special testing requirements, for instance, simulating the breaking capacity of a motor at six times the rated current during startup, or the impact of a bulb load at ten times the surge current.
A full-cycle Life extension strategy
To extend the service life of micro switches, full-cycle management from selection to maintenance is required. When selecting the type, choose the appropriate contact material based on the actual load: gold-plated contacts can be selected for micro current scenarios, while silver-plated contacts are recommended for conventional loads. Models with normally closed contacts often have stronger breaking capacity. In terms of circuit design, for DC inductive loads, diodes with a reverse withstand voltage of ≥10 times the power supply voltage can be connected in parallel to suppress arcs. For AC loads, it is recommended to install an RC absorption circuit (with a capacitor of 1-0.5μF and a resistor of 0.5-1Ω). In terms of the usage environment, the temperature should be controlled between -25 ℃ and 70℃. For dusty environments, products with an IP67 protection rating should be selected. During daily maintenance, the oxide layer on the contact surface can be cleaned with anhydrous alcohol every quarter. When operating, avoid doing it too fast (exceeding 500mm/s) or too slow (less than 0.1mm/s) to prevent mechanical shock or poor contact.
Conclusion
It is worth noting that in recent years, the industry has continuously broken through the lifespan limit through material innovation and structural optimization. For instance, micro switches with titanium alloy reed blades have a mechanical life of over 10 million times. Some enterprises have increased the stability of the switch by 30% through patented guided structure design, effectively reducing the wear and tear caused by operational shaking. For equipment manufacturers and end users, paying attention to these technical details and implementing maintenance norms can significantly extend the service life of micro switches, reduce equipment downtime maintenance costs, and provide a fundamental guarantee for the reliable operation of industrial automation and intelligent equipment.
Post time: Jun-05-2025